The Stuttgart Media University (HdM) used the last two years intensively to give its three film and TV studios in the Electronic Media faculty a technical makeover: With the help of Rosco, SOMMER CABLE and MA Lighting, among others, it now offers state-of-the-art technology for the next generation.
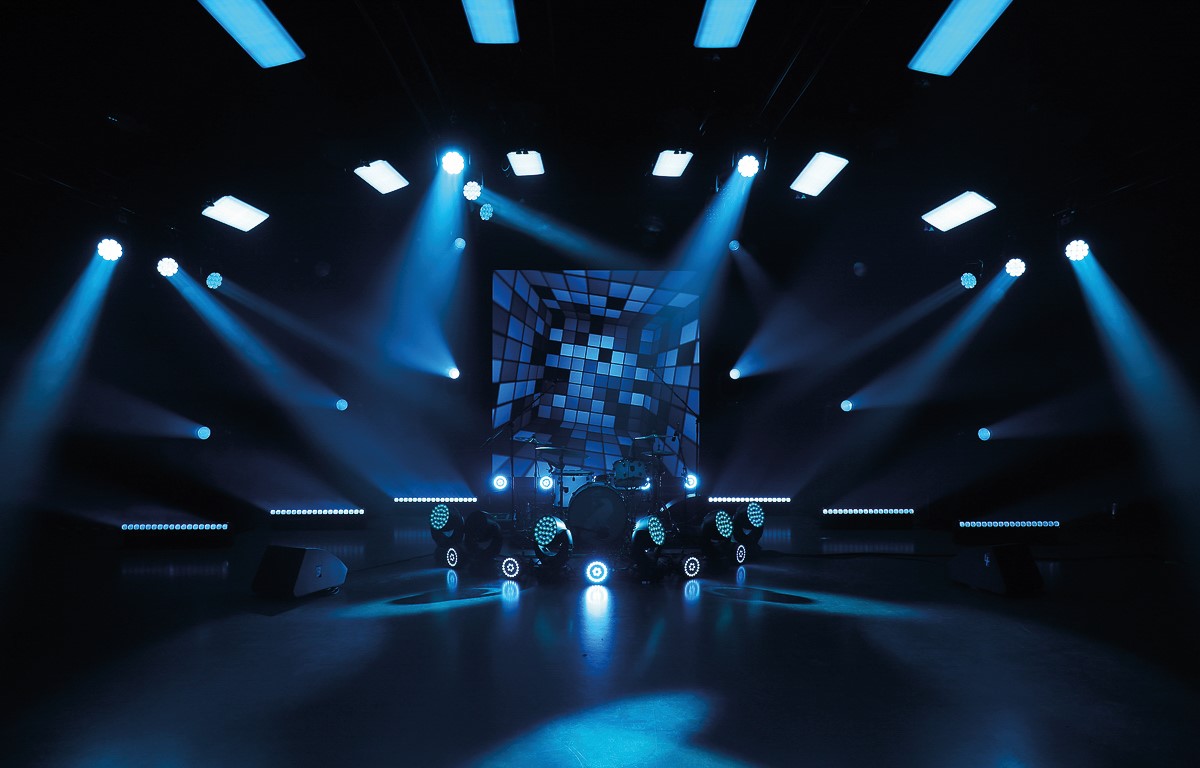
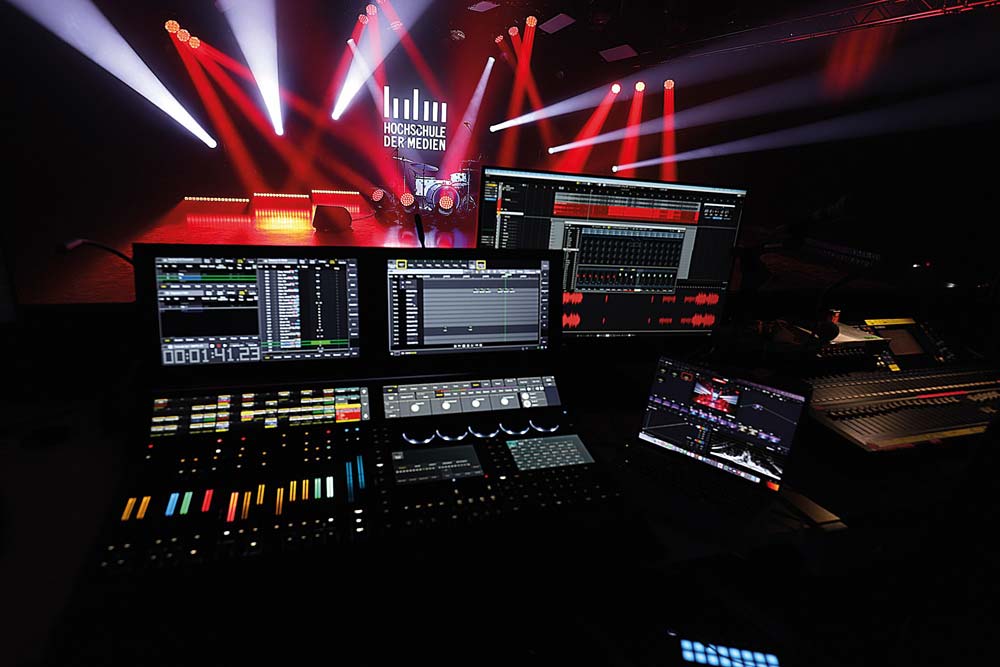
“We wanted to make our facilities fit for the digital and sustainable future
of film and television. Since the start of lectures last summer, students
have been able to use the new studios for their productions,” says
Matthias Bürgel, staff member of the audiovisual media study program
and responsible for equipment selection in the tv production area.
Stuttgart Media University (HdM) is a state university sponsored by the state of Baden-Württemberg. With around 30 accredited Bachelor’s and Master’s degree courses, it covers all areas of media. This includes the Audiovisual Media course, which provides practice-oriented education in the fields of film, tv and media studies. In particular, research in the areas of high dynamic range, wide color gamut and higher frame rates at the HdM Stuttgart has attracted international attention. A total of around 5500 students are currently enrolled at the university.
The three studios are the most frequently used studio areas for live television production, for image recording for visual effects and film production and for the realization of interactive experience spaces. The ceiling infrastructure and lighting technology of all studios was to be fundamentally modernized in order to be able to map contemporary workflows and lighting concepts in teaching and research. In future, current topics such as the digital control of lighting systems, pixel mapping, lighting design with moving heads and the programming of lighting design concepts can be implemented in teaching. “From now on modern LED lighting technology, the latest control technology and motorized traverse systems are available. For the first time, we are able to work very flexibly with moving heads, beamers, camera and tracking systems from above. When renovating the studios, we focused on sustainable, energyefficient aspects in order to generate a lower heat load during our productions,” explains Bürgel.
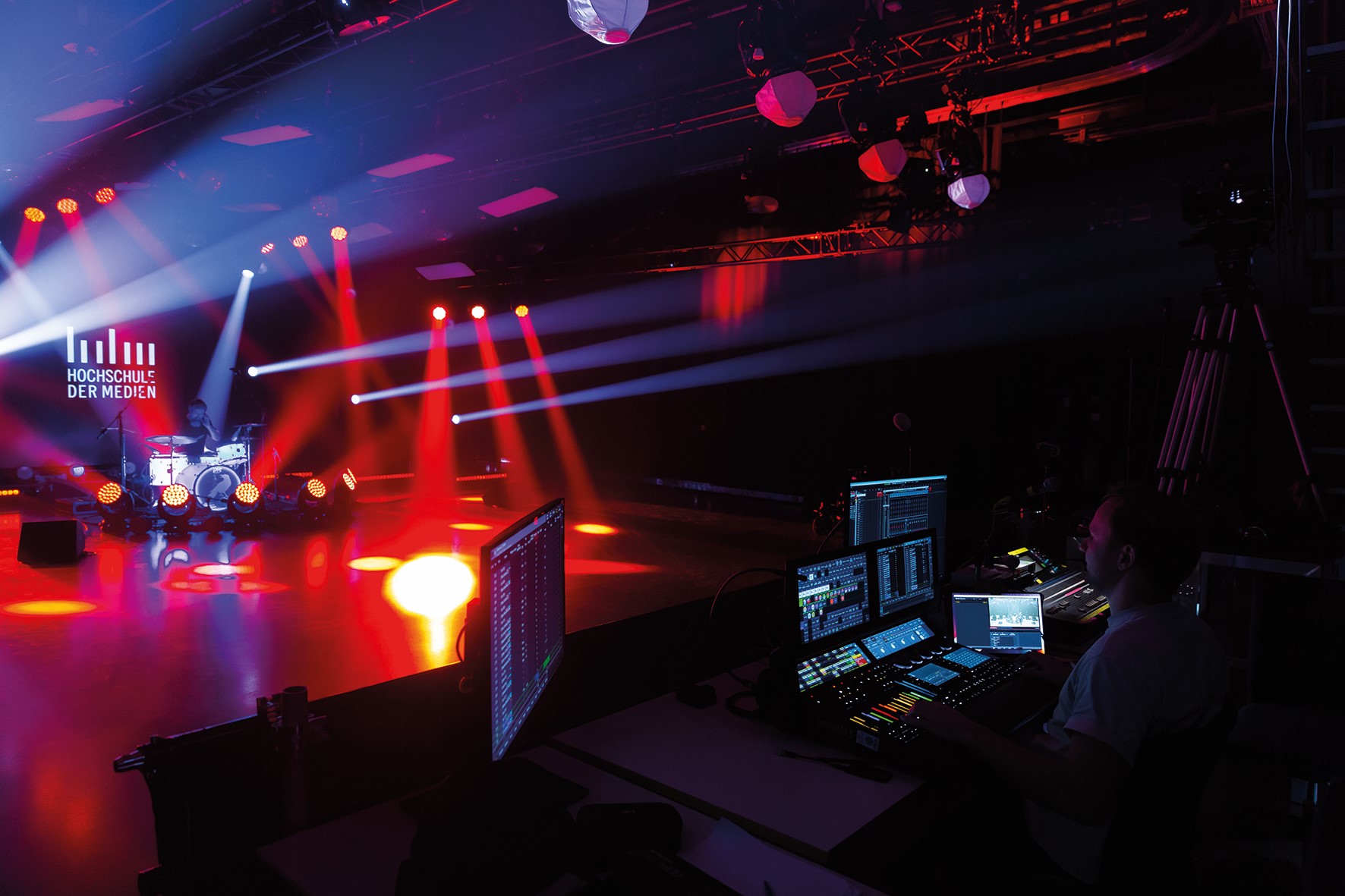
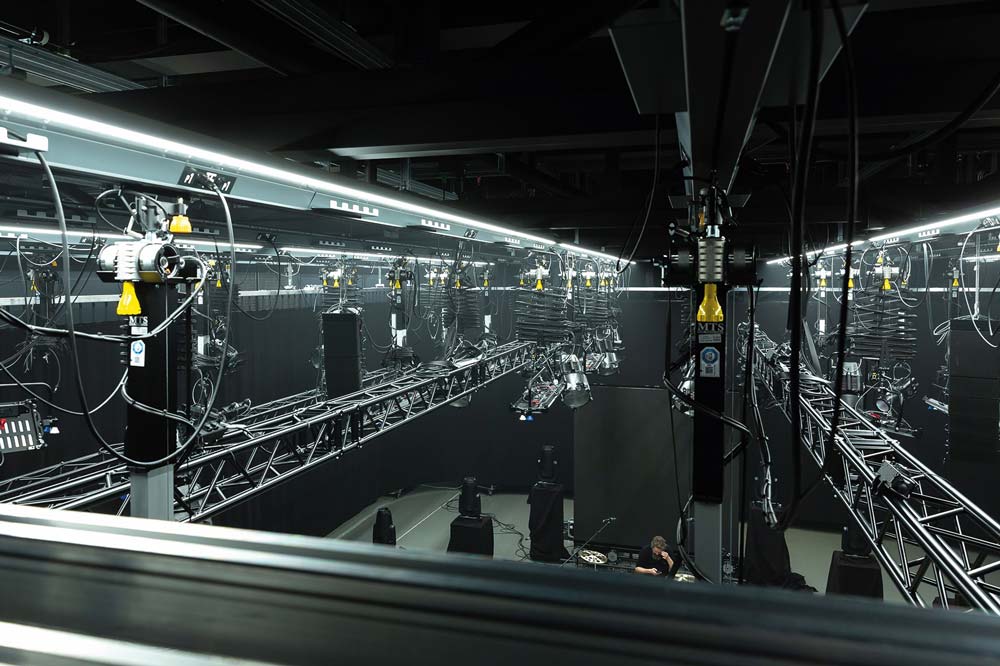
The ceilings first had to be completely gutted for the renovation. The air conditioning technology and the electrical and data cabling for the lighting systems were replaced in all studios. “The cabling was still from the time our studios were built (1999/2000) and was designed exclusively for load dimmers and not even networked in any structured way with regard to DMX. Of course, we wanted to change this and developed a concept for a completely new network structure in all production studios,” explains Simon Hermentin, responsible for the film production area at the Hochschule der Medien.
“The conversion of the studio ceilings therefore included a new network infrastructure to enable IP-based integration and control of lighting, audio and video data in the future. Not only the growing number of device parameters, but also the integration of a media server, LED video walls and other control computers made this transition to IP-based network protocols in lighting control urgently necessary. The new lighting network in all studios consists of a self-contained LAN. Spotlights are currently controlled via the Art-Net protocol. ‘Power over Ethernet’, another Ethernet standard, has also been implemented in the studios. This technology enables the integrated transmission of data and power within a network, allowing us to operate even small components without an external power supply in the future, using Netgear switches from the 4250 AV-Line with PoE++,” continues Hermentin. The entire cable technology comes from SOMMER CABLE.
Following the conversion, all studio ceilings are now wired with Ethernet. In addition to the lighting network, there is a second network on separate patch panels. This spare network is intended for all patches of devices that do not originate from the lighting area, for example if a setting is not to run via switches but “point to point“. The studios and all associated equipment rooms are also using fiber optics, so that applications can be implemented relatively easily between the rooms and in mutual use.
The hall lighting was also replaced for set-up work and seminar operations. This also applies to the support systems on the ceilings and their coordination with the building statics. Current fire protection measures were taken into account for all studio areas. All rails, ceiling offsets and wall offsets are supplied with load multicore in order to be up to date in terms of energy technology. “We used Stagesmart C24 distributors in between to supply each circuit with RCBO. This also makes tracking very easy in the event of a fault. We also receive an exact data record of our consumption and can follow the utilization of our power circuits live – an excellent thing for teaching!” In this new system, there are always six circuits at each offset – whether rail, WAK or ceiling - either as PowerCon True 1, as Socapex or doubled in parallel.
“Peter Rieck from SOMMER CABLE and DP Lighting Systems in particular
provided us with a great deal of support from the specification stage
through to implementation. Sommer cable has been a reliable supplier to
our universiy for many years. After an extremely detailed planning exchange,
we quickly realized that we had found the best tailor-made solution
with the Sysboxx and Systrunk components: an expandable, modular
system from which our distribution boxes are built in a robust, discreet
and stable sandwich construction. And: you have insert plates for
every conceivable plug contact with the best quality.”
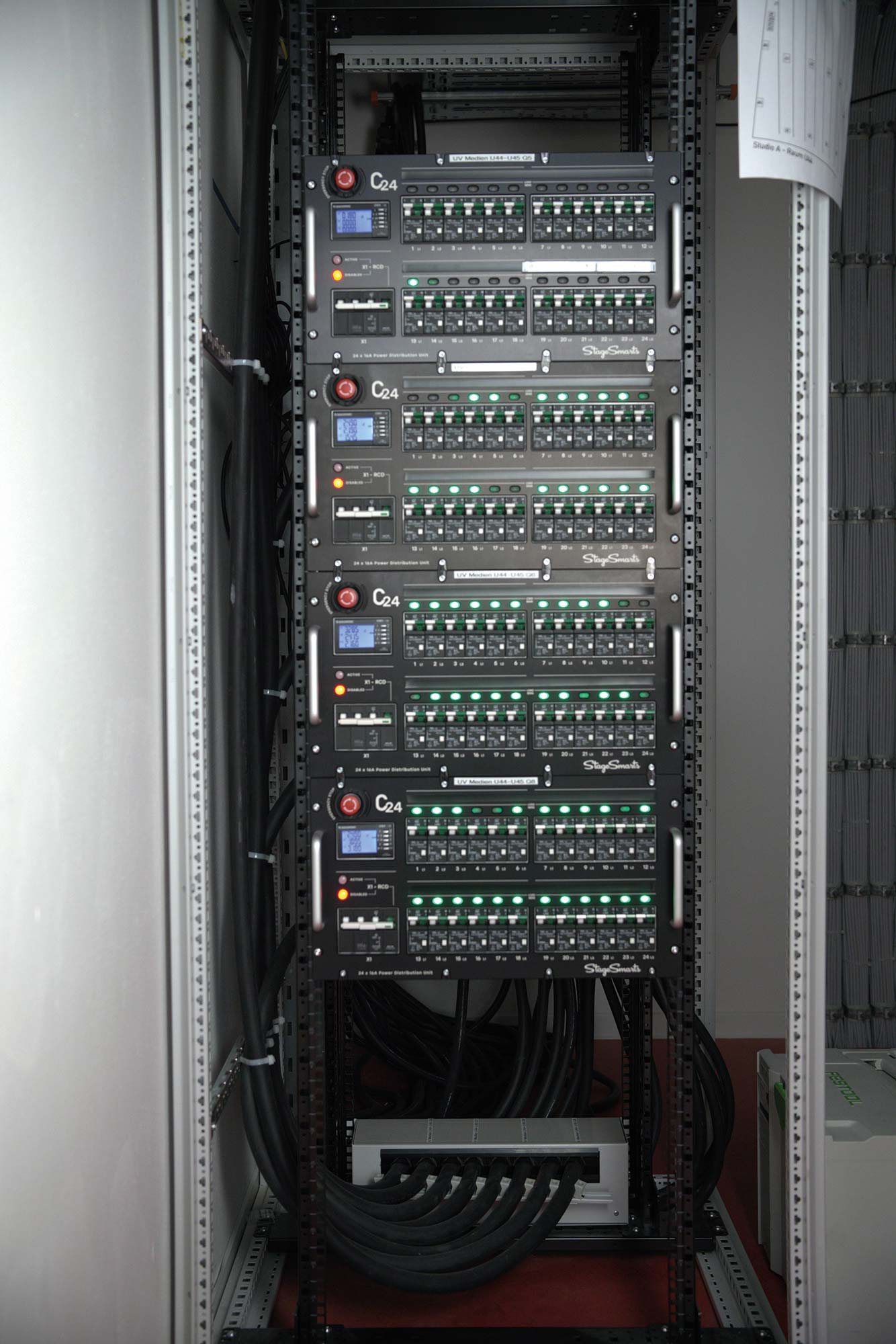
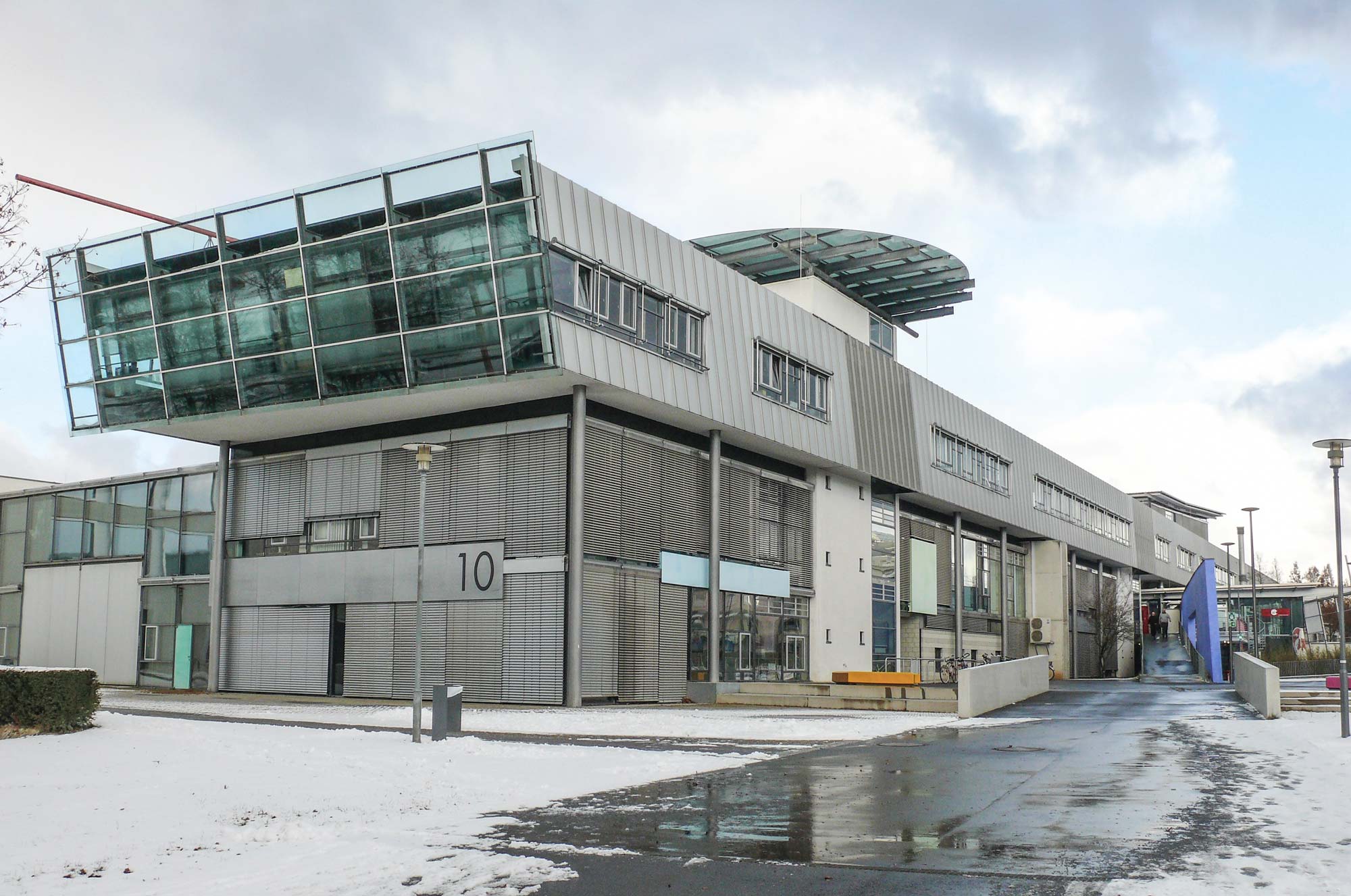
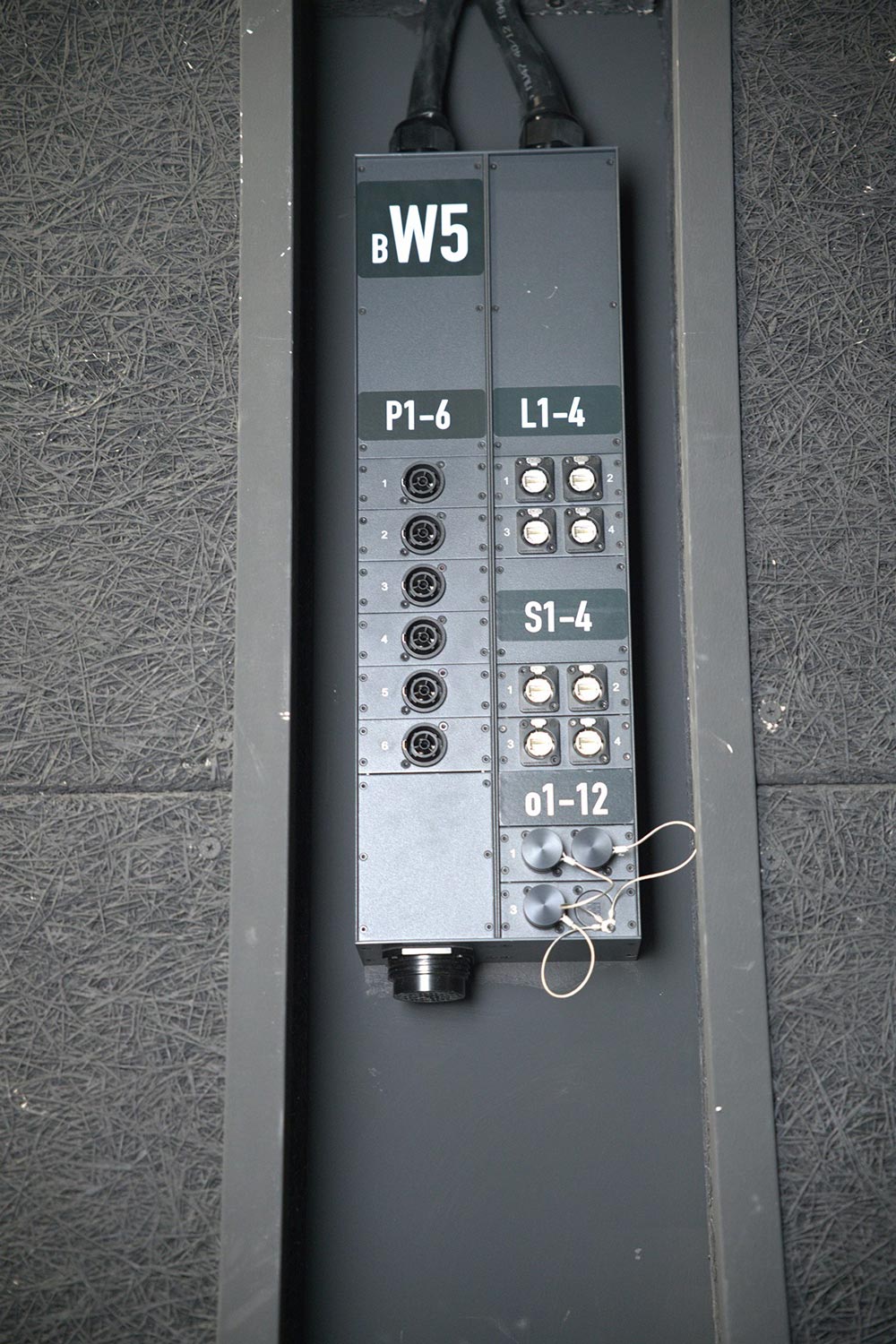
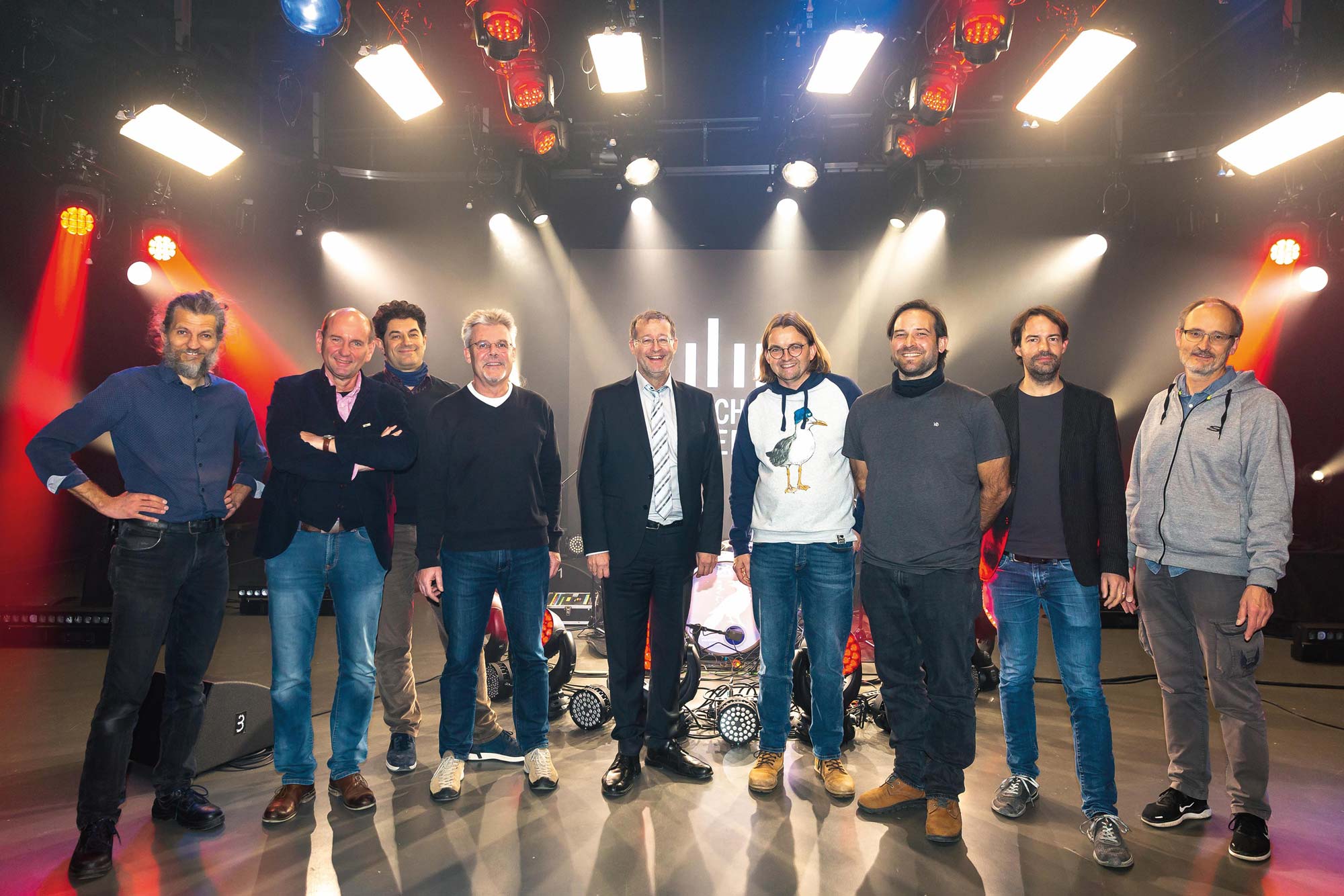
Matthias Adler (Produktionsingenieur TV), Prof. Dr. Burkard Michel (Dekan der Fakultät 2 Electronic Media), Prof. Stefan Grandinetti, Matthias Bürgel (Produktionsingenieur TV), Prof. Dr. Alexander W. Roos (Rektor), Peter Ruhrmann (Produktionsingenieur VFX), Simon Hermentin (Produktionsingenieur Film), Prof. Dr. Jan Fröhlich und Steffen Mühlhöfer (Produktionsingenieur Event Media).
The HdM also purchased Rosco Mixbooks to support the teaching process. With these handy, digital color sample books and a corresponding free app, different color and lighting variants can also be tried out outside the studio or set and saved in the app. All settings can later be transferred to all Roso surface lights via the app.
In addition to Rosco, other luminaires from Arri and Robe were used: “At Arri, we invested extensively in Orbiter and the entire range of optical attachments. We were completely convinced by the Orbiter as a pointsource spotlight due to its versatility, outstanding connectivity and color quality,” says Simon Hermentin, explaining the choice. T1&T2 Profile moving lights, LEDBeams 350 and Tetra Bars from Robe are now being used. „For the profiles in particular, it was important to us that they could keep up with the Arri and Rosco spotlights in terms of white light quality,” says Hermentin.
He continues: “With the Profilers, we also like to work with Lightbridge reflectors in the scenic area. The Cine Reflect Lighting System enables us to work very precisely, unobtrusively and spill-free. As a large ‘single source’ for the scenic area, we rely on three Sumomax in the socalled ‘Super3 Yoke’, with which it is possible to mount the honeycombshaped spotlights directly next to each other and thus create a homogeneous light field. The lights are also capable of pixel mapping – useful for virtual productions.”
The conversion of the studio ceilings also included a completely new electrical and network infrastructure. “As we no longer have any dimmers in use following the complete migration to LED technology and also wanted to be equipped for future studio scenarios, it was an obvious decision to implement the entire lighting control system as network-based only via sACN and Art-Net. This was the best time for us to switch to grandMA3 lighting consoles in both the tv and film studios,” explains Bürgel. The decision was ultimately made in favor of the grandMA3 light and the grandMA3 compact. “When planning larger tv productions, but also virtual sets, the topic of pre-visualization has become increasingly important. In combination with the Vectorworks and Depence 2 applications, the consoles offer an excellent working basis for this.”
Network- and motor-controlled lighting systems open up new approaches that expand and change current design and production conventions in the fields of tv, film/VFX and event media. Simulations of spatial movement through moving lights are now possible, especially for filming visual effects productions in the studio. By synchronizing cameras and LED background images, improvements can be made to motion simulations and the sense of space. “This is a further step in learning the latest media productions,” says Prof. Dr. Fröhlich.
The Event Media Studio at the HdM has become “intelligent” thanks to technical installations with sensory units and microcontrollers. They make installations responsive, reactive and mobile. “The new structural and suspension mechanics enable a whole new learning world for the construction and design of interactive media experience spaces,” says Steffen Mühlhöfer, Head of Studio Productions, adding that not only the studios have been renovated in terms of stage technology, but the sound system in the HdM cinema “Hardcut” has also been acoustically optimized.
Other companies involved included Movecat, Hof Alutec, Cast, ICT, Trendco, Lightequip, Contrik, MTS and Sumolight. Fire protection, HLS, acoustics and electrics were coordinated by the architectural firm Plan7. Jürgen Kössinger (Wireworx planning office, Stuttgart) provided support with the preliminary coordination and project management.
The conversion costs amounted to around 1.3 million euros. They were
financed via a large-scale equipment application to the German Research
Foundation and from university funds. Outside of the application budget,
a major fire protection measure was also carried out, the room acoustics
were adapted in the studios, ventilation technology was converted and the
entire electrical work was also covered by the budget of the responsible
university building department.